不銹鋼吹氧脫碳過程的速率現(xiàn)象基本上與一般鋼液相似,亦分成三個階段。其主要特征是:由于存在大量的鉻,因而要求更高的反應(yīng)溫度和更高的平衡含氧量。 因此在不銹鋼吹氧脫碳時,高碳范圍內(nèi)供氧強度對脫碳速度的影響,比起碳鋼來更為明顯。 因為若無一定的供氧強度,鋼液升溫速度就不能適應(yīng)鋼中鉻碳比不斷變化的要求,吹入的氧將大量用于氧化鉻和鐵,而不是碳。顯然,在不銹鋼吹氧脫碳時,存在一個可保證進行選擇性脫碳的臨界供氧速率。供氧速率只有大于此臨界速率,方能實現(xiàn)降碳保鉻,使鋼液中碳含量不斷降低、而在此速率以上,繼續(xù)提高供氧強度可加大脫碳速度、減少鉻的燒損。 臨界供氧速率是鋼中含鉻量及爐子容量(與熱損失速率有關(guān))的函數(shù)。爐料中配入的鉻越高,爐子噸位越小(熱損失大),相對要求更大的供氧速率。但供氧速率過大時,吹入氧氣的利用率會降低,從而有可能使脫碳速度下降。故對于一定尺寸的爐子,在一定原料條件下,應(yīng)有一最佳供氧速度。對于8噸電爐精煉不銹鋼來說,最佳供氧速率和吹氧管直徑有關(guān)。在同樣供氧速度時,若采用較細(xì)的吹氧管,則吹氧壓力必然要提高;而過大的吹氧壓力,對于淺而平的電爐熔池來說,將導(dǎo)致產(chǎn)生氧氣不能充分利用的問題。 因此,當(dāng)采用直徑1/2英寸的吹氧管時,最佳供氧強度為40英尺
3/(分·英噸);而當(dāng)把吹氧管直徑放大到1英寸時,此最佳值可提高自到55~60英尺
3/(分·英噸)。 對應(yīng)的脫碳速度也由0.11%C/分提高到0.14%C/分。此例說明,在已具有一定吹碳壓力的條件下(如PO
2≥7~9大氣壓),要進一步提高脫氧速度,采用擴大吹氧管管徑或增加吹氧管數(shù)目的辦法,將比采用提高吹氧壓力的辦法效果更好。
對于不同容量電爐來說,脫碳所需的吹氧壓力也各不相同。曾有人研究了100噸電弧爐冶煉不銹鋼時,氧氣壓力及供氧速率對脫碳速度的影響,發(fā)現(xiàn)在爐容量大及[C]大于0.15%的情況下,提高氧氣壓力對改善熔池中氧的傳遞(鋼液攪拌)有明顯的作用,可提高脫碳速度;而供氧速率>30米
3/(小時.噸)以后,其對脫碳速度的影響就不很明顯了。
關(guān)于真空下吹氧使不銹鋼脫碳的動力學(xué)研究表明,溫度愈高,壓力愈低,則反應(yīng)的速度常數(shù)K的值愈大,如圖右所示。
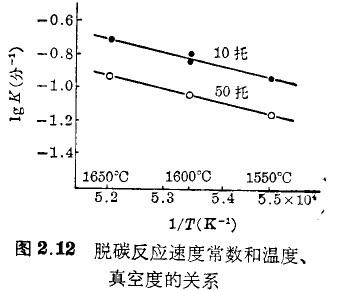
另外,在頂吹純氧的條件下對真空下脫碳反應(yīng)進行的詳盡研究表明,在高碳區(qū)域內(nèi),脫碳反應(yīng)的限制性環(huán)節(jié)主要是氧氣的供應(yīng),其次是鋼液面上生成的氧化膜對脫碳反應(yīng)的影響。在低碳區(qū)域內(nèi),脫碳速度大體上隨含碳量的減少而成比例地減小,如圖右所示,

脫碳速度常數(shù)K與壓力和鉻含量之間并未顯示出明顯的對應(yīng)關(guān)系。這些事實表明,不銹鋼低碳區(qū)域的脫碳反應(yīng),也是受鋼液中碳的擴散支配的。
圖
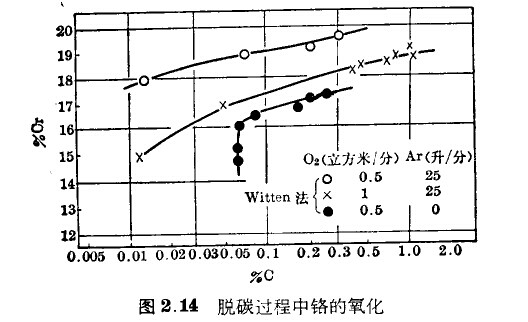
示出了用1噸VOD試驗裝置進行
不銹鋼工程上常用鋼材18-8型不銹鋼脫碳試驗的結(jié)果。從圖可以看出,在低碳區(qū)域內(nèi)的脫碳過程中,影響鉻氧化的主要因素是攪拌和過剩氧,因此采用氬氣攪拌脫碳,可以防止鉻的氧化。